安全性の高い、高品質なサン・クロレラAを世界の多くの人々の健康づくりに役立てたい―。
その想いを実現するために、当社独自の製造基準と規格基準に基づく厳密な生産管理・工程管理・品質管理を実施しています。
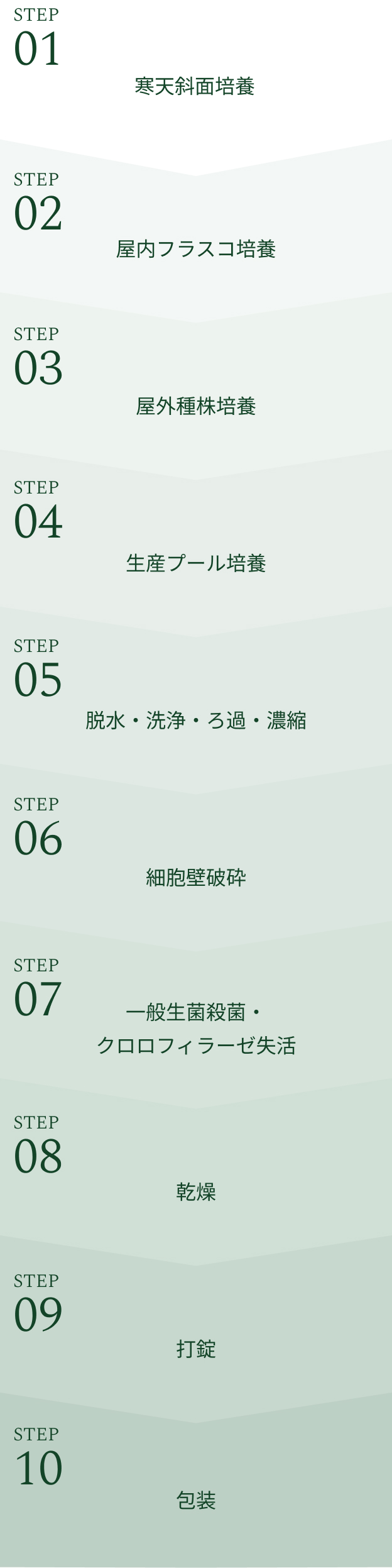
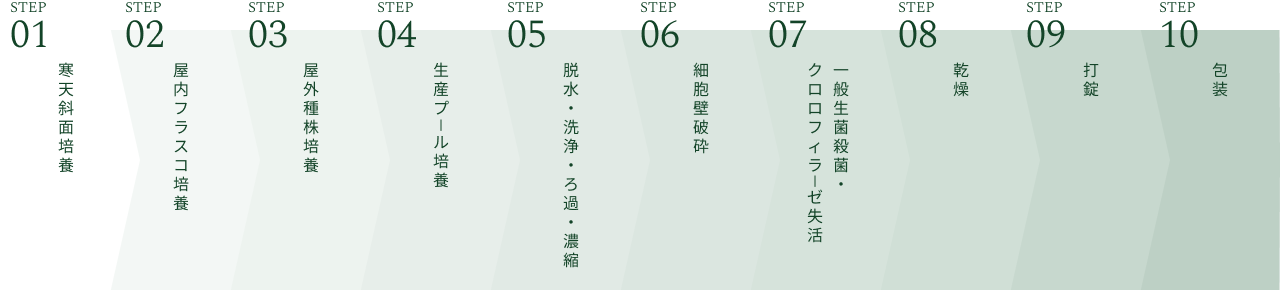
- 01
-
寒天斜面培養
保存株クロレラ・ピレノイドサ種(サン・クロレラ株)を寒天斜面培地に移した後、光(人工光線)を当てて、最適温度条件下で増殖させます。
- 02
-
屋内フラスコ培養
寒天斜面培養で増殖したクロレラを液体培地の入った扁平フラスコに移し、炭酸ガスを含んだ空気を供給して光を当て培養します。培養液中のクロレラの濃度が高まってきたら、順次大きなフラスコへ移し、培養を続けます。
- 03
-
屋外種母培養
フラスコを屋外の攪拌機付きコンクリート製円形プールに移し、自然環境下での培養を開始します。クロレラは円形プールの中で、太陽光線を浴びながら増殖を続けます。クロレラの濃度が高まると、より大きな円形プールへと移していきます。
- 04
-
生産プール培養
直径36〜46mの攪拌機付の円形プールの中で、太陽光がまんべんなく当たるように常に攪拌します。温度条件、太陽光の照射条件に合わせて、きめ細かく培地(クロレラの栄養分)の供給量をコントロールしながら培養を続けます。培地には、3000m級の山を水源とし、清浄で汚染が無く、硬度が低い上に質・量ともに安定した地下水を使用しています。自然環境下で屋外培養することで、タンク培養品とは異なり、ビタミン B12を豊富に含んだクロレラになります。
- 05
-
脱水・洗浄・ろ過・濃縮
生産プールで培養されたクロレラは、所定の濃度に達したら収穫。培養液中に混入した異物をフィルターで除去した後に、遠心分離機で脱水・洗浄を繰り返し行い、さらにろ過、濃縮します。
- 06
-
細胞壁破砕
クロレラは細胞壁で守られていますが、この細胞壁が強靭すぎて、成分を有効に摂取できないという欠点がありました。これについては当社が開発した細胞壁破砕法により解決。ダイノ-ミルという機械で、細胞壁を物理的に破砕します。シリンダーには剛性球体が入っており、クロレラスラリーと共に攪拌されます。その際、攪拌液中に部分的な圧力差が生じ、クロレラ細胞が急激に膨張し、破裂することによって細胞壁が破砕されます。
- 07
-
一般生菌殺菌・クロロフィラーゼ失活
クロレラには、光過敏症の原因物質 (フェオフォルバイド) をつくるクロロフィラーゼという酵素が含まれています。この酵素の失活と殺菌を行うために、クロレラスラリーにスチームを混合し、短時間高温処理を施します。
- 08
-
乾燥
クロレラは乾燥させることで水分活性が低下し、長期保存が可能になります。
一般に、クロレラの乾燥にはスプレードライヤー法が幅広く採用されています。熱風が供給されたスプレードライヤーに、クロレラスラリーを噴霧すると、瞬時に乾燥します。
生のクロレラは腐敗しやすいのですがこのようにして品質を損なうことなく手早く乾燥させることで、鮮緑色で青のりや抹茶のような香りがする粉末状の乾燥クロレラができます。
この乾燥クロレラは適切な条件下であれば、数年保存することが可能で、品質の低下も見られません。
- 09
-
打錠
打錠機を使用し、成形加工しています。製造した製品は、外観検査、重量検査、異物検査、細菌検査、物理特性検査、成分分析検査を行います。また、重要な成分については、公的規格より厳しい自社規格を設け、公的機関で試験を行うことにより、厳重な品質管理を実施しています。
- 10
-
包装
すべての検査にパスした錠粒をアルミパックに入れて包装し、サン・クロレラAが完成します。
以上のような厳密な生産管理・工程管理・品質管理を実施して製造したサン・クロレラAを、世界の多くの人々の健康づくりに役立てようと日々努力しています。
製品化
安心して飲用できる確かな製品をつくるために、
サン・クロレラAは(公財)日本健康・栄養食品協会の定めるGMP基準に合格した認定工場で製造しています。
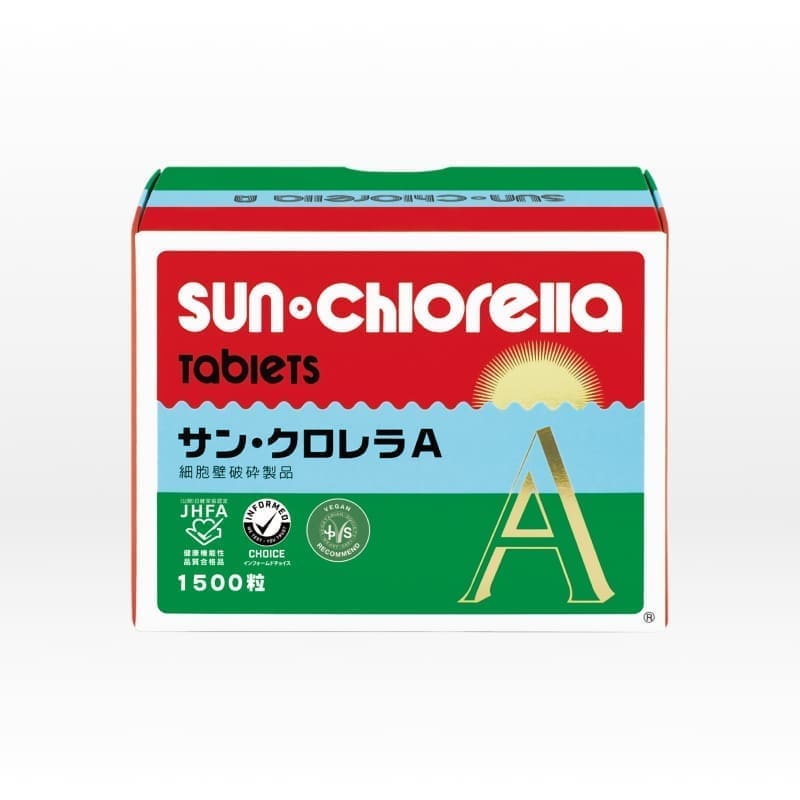
GMPマーク
Good Manufacturing Practiceの略で、「適正製造規範」といいます。原材料の受け入れから最終製品の出荷に至るまで、適切な管理組織の構築及び作業管理(品質管理、製造管理)の実施(GMPソフト)と、適切な構造設備の構築(GMPハード)により、製品の品質と安全性の確保を図る目的で制定されました。
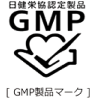